Why Do Adaptive Robots Excel at Material Abrasion?
In manufacturing, material abrasion tasks such as polishing, sanding, and deburring are essential steps in product transformation. Flexiv’s adaptive robots are ideal for surface treatment applications because they can ‘feel’ the surface they are interacting with.
Powered by whole-body force control and 1 kHz contour tracking capabilities, adaptive robots bring human-like sensitivity and precision to industrial applications. This adaptive advantage allows customers to automate previously impossible tasks while reducing the total cost of ownership through the use of standard power tools, shortened commissioning times, and improved solution flexibility.
Why Is Material Abrasion Difficult to Automate?
Replicating a manual surface treatment process requires more than just motion; it demands human-like dexterity and the ability to maintain a consistent force on a surface while adjusting to irregularities.
While traditional collaborative robots can be configured for material abrasion tasks, doing so typically requires expensive force-sensing end-of-arm tools, specialized equipment, and extensive programming.
Surface Treatment Bottlenecks for Traditional Solutions

Force Control
To achieve an acceptable surface finish, a precise combination of force control and positional accuracy is essential.

Customized Solutions
Each workpiece, whether it's being sanded or polished, requires unique trajectory tuning. This increases changeover time and overall system downtime.

System Complexity
Traditional automated abrasion solutions require more than just a robot. They often need a force-sensing flange and a specialized end-of-arm tool, leading to higher complexity and cost.
Diverse Grinding Needs
Grinding tools can vary from being passive, motorized, or even pneumatic, depending on the workpiece’s parameters such as size, curvature, or angularity. This variety demands different tools and techniques for different tasks.

Flexiv’s adaptive robots simplify the material abrasion process by fusing industrial-grade force control, artificial intelligence, computer vision, and intuitive programming into a universal surface treatment solution that offers automatic trajectory tuning and the ability to utilise off-the-shelf tools.
How Flexiv Creates a Flawless Finish
To deliver a surface finish equal to or better than possible with manual labor, Flexiv’s adaptive robots utilize the following technologies:
Contour Tracking & Trajectory Learning
Originally developed in 2019, Flexiv’s contour tracking algorithm has evolved into a full trajectory learning capability. This allows the robot to precisely follow complex, curved, or concave surfaces.
As the robot begins a task, it records its positional and force feedback data in real time. After collecting trial data, it then automatically updates its control strategy using self-learned parameters.
Curved Surface Tracking
Whole-body torque control enables the robot to maintain constant contact with any surface, regardless of curvature.
Hybrid Motion & Force Control
An adaptive robot can reach speeds of up to 1000 mm/s during linear sanding, all while maintaining a force control accuracy of 0.6 N.
Disturbance Rejection & Dexterity
Material removal processes generate unavoidable disturbances, be them from the workpiece itself, the workbench, tools, or nearby machines. Adaptive robots counter this interference using built-in torque sensors in each joint.
With seven degrees of freedom, Flexiv’s Rizon robot mirrors the dexterity of a human arm, enabling precise compensation and robust performance.
How Does an Adaptive Robot Excel at Material Abrasion?
There are multiple reasons why adaptive robots are superior for material abrasion tasks, but here are the top four:
Unmatched Versatility
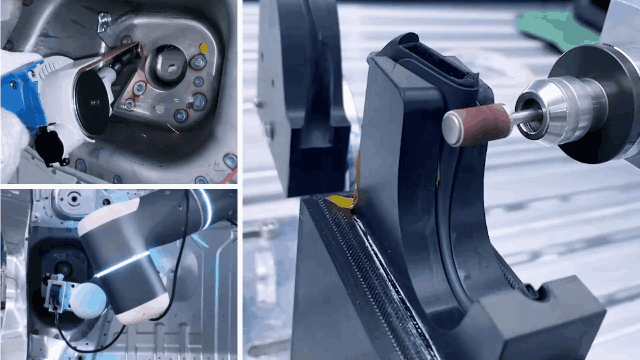
An adaptive robot dynamically adjusts the force it applies, enabling it to switch between heavy-duty and delicate tasks. Whether sanding a guitar body or polishing granite countertops, the same robot with standard tooling can be used. This maximizes floor-space efficiency and line changeover speed, while reducing hardware sprawl.
Superior Quality & Consistency
With optional self-learning algorithms, an adaptive robot can not only complete tasks efficiently, but it can continuously improve its performance.
Real-time sensor feedback ensures optimized material removal, consistent surface finishes, reduced risk of damage, and less wear on consumables.
● In smartphone polishing, Rizon maintains a 1 N accuracy and limits fluctuations to just 2–3 N. ● In complex insulator grinding, it consistently achieves 1–2 N force accuracy.
Effortless Deployment
Thanks to Flexiv’s intuitive and powerful graphical programming interface, Elements, programming an adaptive robot is as easy as dragging and dropping action blocks into a sequence.
Tasks can be created and simulated in a high-fidelity virtual environment, either online or offline, enabling an adaptive robot to be up and running inside of an hour.

This easy-to-use system enables rapid deployment, a faster ROI, and greater production agility.
Efficient & Future-Proof
Adaptive robots feature integrated sensors and leading-edge force control technology, which eliminates the need for external sensors or compliant mechanisms. This reduces overall costs and provides a future-proof robotic platform that can be modified on an as-needed basis.
● Lower Upfront Costs: Fewer components to purchase and maintain ● Future Scalability: Easily expand into new applications without replacing core systems. ● Simplified Integration: Reduced commissioning time through unified hardware and software.

Customers typically see up to 50% cost savings when compared to traditional multi-component systems. Further savings are also possible through the external TCP functionality, which enables adaptive robots to utilise existing standalone sanding or grinding equipment.
Beyond Grinding & Polishing
Flexiv’s adaptive robots support sanding, deburring, and other material removal processes that require a sense of ‘touch’.
With Flexiv’s force-sensing know-how, manufacturers can: ● Work with deformable or lightweight materials. ● Apply new finishes and coatings with minimal retooling. ● Rapidly prototype and test new surface processes to stay ahead of market trends.
Flexiv’s ongoing R&D also gives you access to the latest algorithms and deployment tools. This enables you do more with less, while staying ahead of the competition.
Ready to Transform Your Surface Treatment Operations?
Contact our team to schedule a demo or request data for your specific application. Not sure if your use case fits? Reach out to us for tailored advice and support.