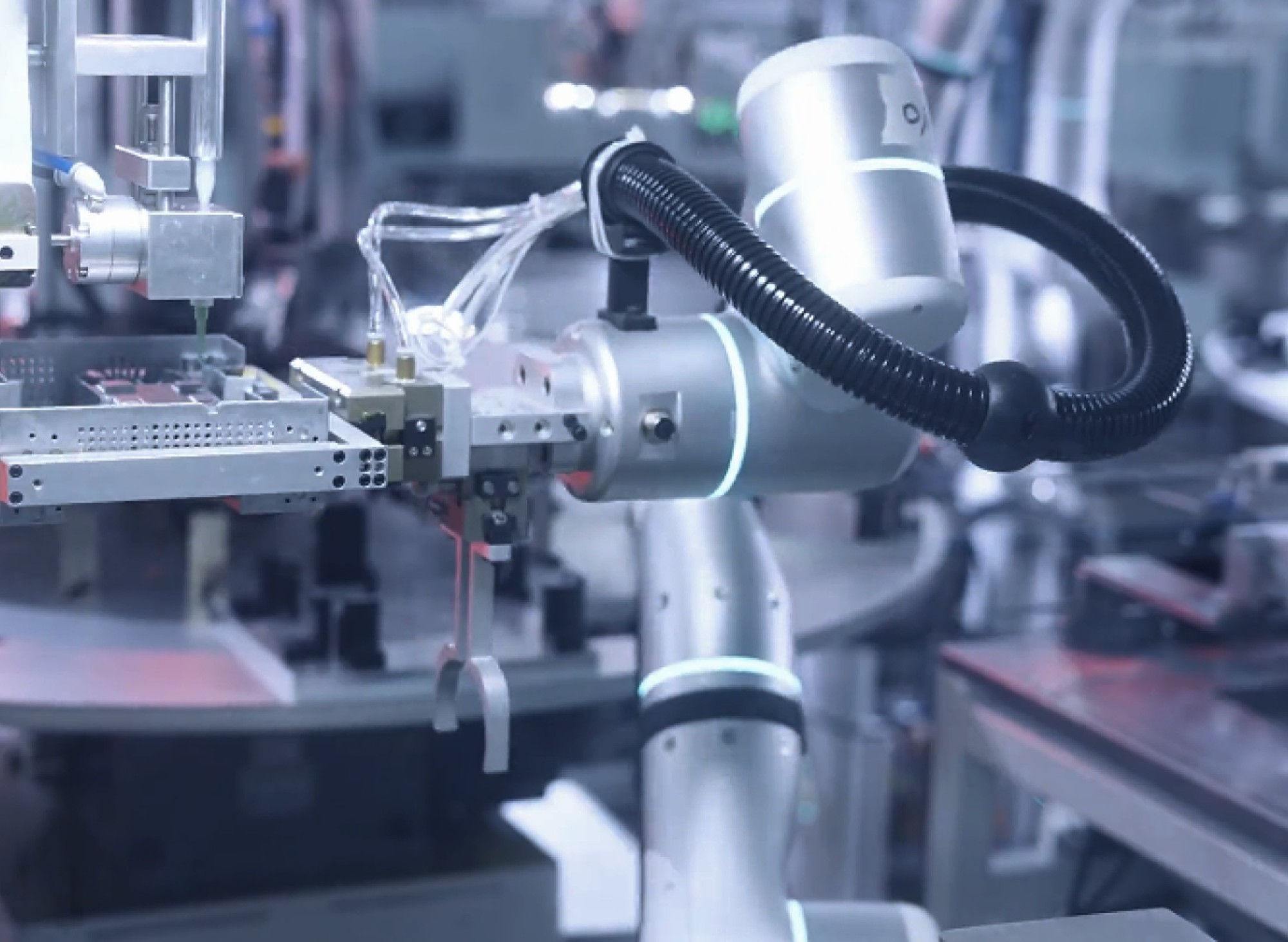
ASSEMBLY AUTOMATION
Bring unmatched versatility and efficiency to your assembly tasks.
Empowered by Flexiv's industry-leading integrated force/torque sensors, adaptive robots can effortlessly automate everything from material loading and screw fastening to precise component alignment and connector installation. What’s more, our intuitive and easy-to-use programming interface allows for the automation of complex tasks and seamless integration within your existing production environment.
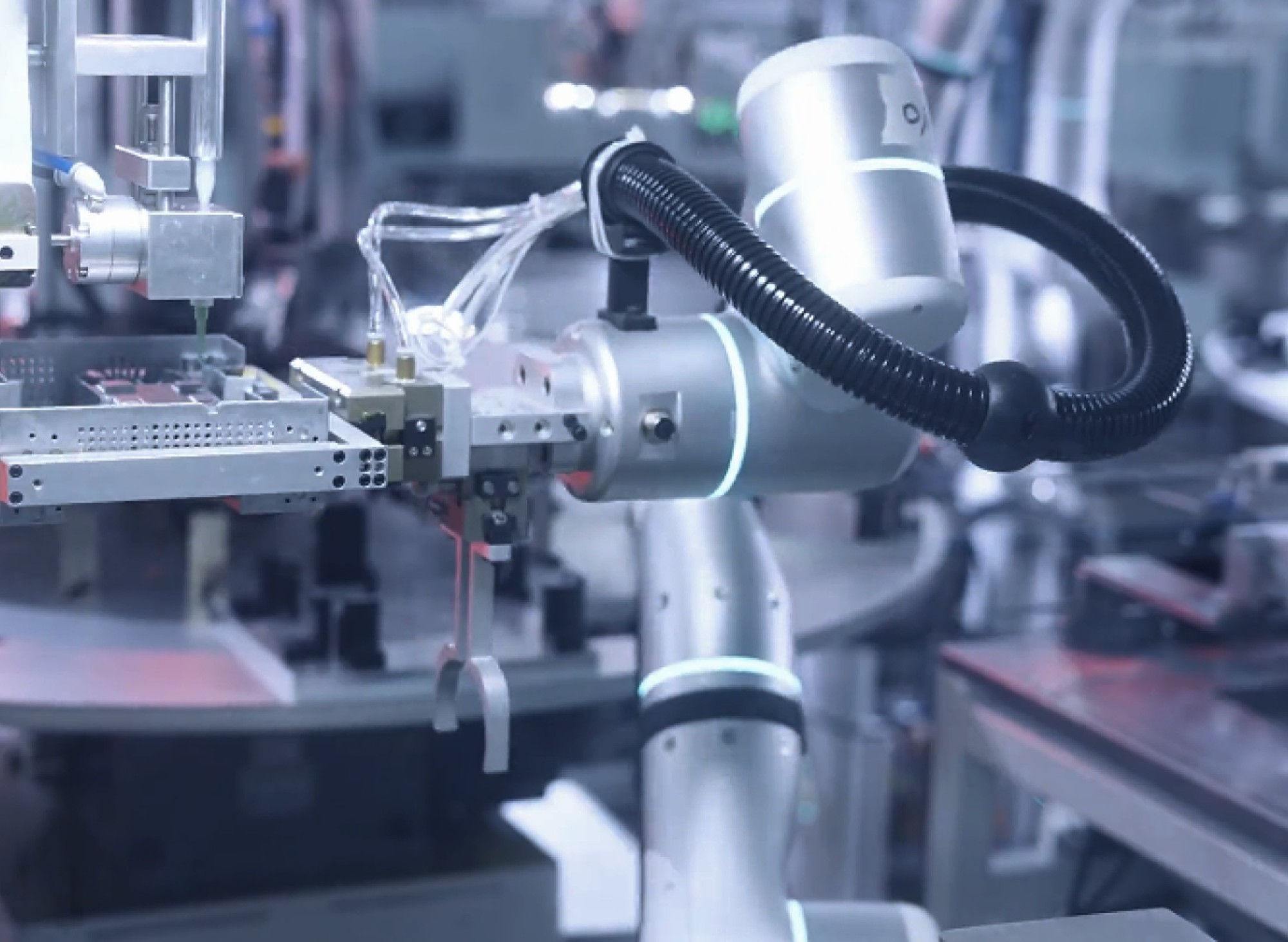
Contact Us
Seeing is believing. See how Flexiv robots can help.
Thank You
Thank you for your request! We’ll get back to you soon. In the meantime, you can find more information on our website and social media pages.
Go to HomeAutomate Everything
Reduced Complexity
Streamline production with an average 56% decrease in supporting machinery.
Continuous Operation
Flexiv’s adaptive robots can run 24/7 in a 'lights out' setting without downtime.
Unmatched Precision
Achieve a repeatability of +/- 0.05 mm and assembly accuracy of +/- 0.01 mm.
Flexiv’s Rizon series of robot arms is the ideal solution for automating even the most challenging tasks. With 7-DoF articulation coupled with whole-body torque control, a Rizon robot can independently handle and insert delicate components with ease.

Unmatched Accuracy
Precise Force Control
Achieve force sensing accuracy down to 0.03N.
Adaptive Assembly
Adjust to workpiece position errors in real-time.
Flexiv's robots excel at assembling FFC and FPC connectors, as they can use a combination of vision and force guidance to ensure accuracy without damaging components. Our 3D vision system identifies, localizes, and tracks connectors, while proprietary force-guided insertion technology ensures secure assembly with a resolution as low as 0.03N.
Dexterous and Intelligent
Shared Intelligence
Flexiv’s robots can work together to coordinate the completion of difficult tasks.
Robust Reliability
IP65-rated and guaranteed to be maintenance-free forever, Flexiv’s range of adaptive robots provides groundbreaking performance.
Superhuman Sensitivity
Whole-body torque control operating at a 1kHz response rate enables superior levels of regulation and precision so that components can be manipulated with an accuracy of +/- 0.01 mm.
Flexiv's adaptive robots leverage force-control technology to enable a human-like insertion motion and superhuman levels of precision. Seamlessly integrated into the production lines of multiple Tier 1 automotive suppliers, they have revolutionized tasks like dashboard assembly, gluing, deburring, detail application, and ECU/ECM assembly.
Mobile Mastery
Effortless AMR Integration
Designed to work with multiple industrial communication protocols, Flexiv’s robots can be seamlessly integrated with all leading AMR platforms.
Precision Perfected
Overcome the inherent position errors of AMR platforms with real-time force guidance to ensure accuracy and dependable performance.
As the demand for machine tending continues to grow, we’ve leveraged our cutting-edge technology to ensure true AMR compatibility. Precision docking is the cornerstone of successful AMR-based tasks, but achieving the necessary level of precision is difficult. While sub-cm level accuracy is often the best that can be expected for an AMR operating in real-world conditions, this small offset can render a task impossible for a traditional position-controlled robot. Flexiv's holistic integration of its robot arm onto an AMR, combined with real-time force guidance, ensures these errors can be compensated for. This breakthrough delivers reliable and secure loading and unloading, redefining efficiency and precision in AMR-based automation tasks.
Request a Free Consultation
Ready to enhance your production capabilities or automate a challenging task? Fill out the form on the right and discover how we can help you achieve your goals.
Thank You
Thank you for your request! We’ll get back to you soon. In the meantime, you can find more information on our website and social media pages.
Go to Home