Automated Adhesive Primer Application in Automotive Assembly
At a glance
Customer
A renowned new energy car company (Subject to an NDA).
Problem
Reliance on manual labor for potentially harmful primer application tasks in automotive manufacturing.
Solution
Flexiv’s adhesive primer application system uses the Rizon 4 adaptive robot and a customized brush in conjunction with a standard adhesive supply system.
Key Features
High-response force control, force-controlled application.
Advantages
Tolerance to workpiece positional errors, consistent results, easy deployment, and scalability.
Overview
Adhesive primer is applied to work surfaces to maximize the bond that forms between the work surface, primer, and adhesive. The primer application process is commonly employed for pre-treating different materials such as metals, non-metals, and polymers before adhesive bonding, and it’s essential in the installation of automotive glass.
Primers are often made from volatile solvents, which are potentially harmful to human health. Despite this, most automotive priming processes are currently performed manually.
Case Study Customer
A Renowned New Energy Car Company (Subject to an NDA)
The customer had previously heavily depended on manual labor during their production process. Faced with challenges such as high labor turnover, recruitment costs, and the desire to enhance production quality and overall automation, they sought an automated solution to apply adhesive primer. They aimed to implement an automatic cleaning and priming station, bolstering their production quality and throughput.
Flexiv’s Solution
Flexiv’s automotive adhesive primer application employs a Rizon 4 adaptive robot, a customized brush, a standard adhesive supply system, and a gluing software package.
This solution does not require computer vision, as the Rizon 4’s hybrid motion and force control maintains a consistent force between the brush and the workpiece, enabling even curved or uneven surfaces to be treated without specialized programming. The solution exhibits high tolerance to workpiece misalignment and can be rapidly deployed into any installation, regardless of size or shape.
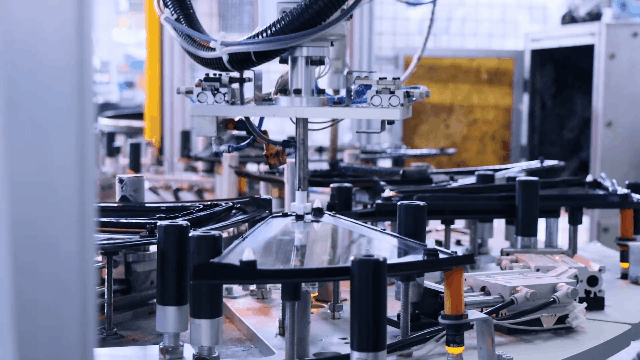
Technical Features
Responsive Force Control
With a 0.1N force sensing accuracy and a 1KHz high-response control frequency, Flexiv’s application solution ensures a constant contact pressure, resulting in a uniform and stable primer quality.
Force-Controlled Application
Real-time feedback and force control from the contact between the robot’s end-of-arm tool and the workpiece enables the surface to be tracked exactly. This allows complex curvatures to be followed and reduces coating breakage and trajectory issues.
Solution Advantages
High Trajectory Error Tolerance
Rizon’s hybrid motion force control counters position disturbances from workpiece misalignment or imperfections, ensuring comprehensive surface coverage and no coating breaks.
Consistent Results
The application has demonstrated a coverage and accuracy rate exceeding 99% in rigorous real-world testing.
Easy Deployment
Users can create gluing paths easily with Flexiv Elements, our drag-and-drop programming interface. This easy-to-use yet powerful software provides operators with unparalleled command and control capability.
Scalability
Fully customizable and infinitely adaptable, Flexiv's adhesive application solution can be seamlessly integrated into any production environment.