Automotive Signal Switch Calibration
At a glance
Customer: A leading automotive supplier (Subject to an NDA).
Problem: The calibration and automated testing of turn signal levers.
Solution: Flexiv designed a testing and calibration system utilizing a Rizon 4s adaptive robot which included scheduling, data collection, communication, IPC, and trajectory planning functions.
Key Features: Real-time data collection, data mapping, trajectory planning, and customizable host control systems.
Advantages: Precise real-time force-sensing accuracy, enhanced safety features, scalability, and improved line-changeover speed.
Overview
The calibration and testing of turn signal levers are critical phases in automobile manufacturing. To ensure the levers operate correctly, Flexiv engineers developed an automotive steering column calibration system. Utilizing the Rizon 4s robot, the system collects data from the TCP (Tool Center Point) and compares it with readings from the steering column's Hall effect sensors. The gathered data is then mapped and confirmed by the steering column sensors to guarantee accurate calibration and functionality.
Customer Profile
The customer is a leading automotive supplier, providing a wide range of OEM products to the automotive industry.
The customer approached Flexiv to automate the labor-intensive process of manual steering column testing. Due to the proximity of the testing site to staff members, the customer emphasized that the solution must prioritize safety and facilitate seamless human-robot collaboration.
Flexiv's Solution
Employing the adaptive Rizon 4 robot and the Flexiv Robot Development Kit (RDK), Flexiv engineers developed a comprehensive steering column lever testing and calibration system. This system encompasses modules for scheduling, data collection, communication, memory, IPC (Inter-Process Communication), and trajectory planning.
During testing, the robot follows a planned trajectory to evaluate the steering column's functions. As each lever is activated, the robot’s end position and force data are captured in real-time and synchronized via an SPI (Serial Peripheral Interface). Should the robot identify a fault in the steering column, the event is flagged, and the production manager is automatically notified.
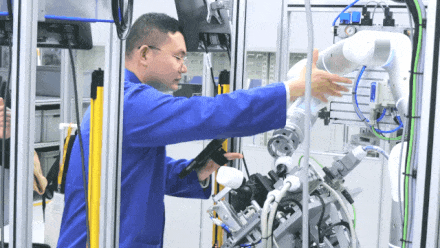
Technical Features
Real-time Data Collection
The Flexiv RDK gathers and transmits data concerning the robot's end TCP position and the external forces experienced by the robot when it activates a steering column lever function.
Robot Motion Planning
Utilizing standard numerical modeling and kinematic trajectory planning, the system ensures precise end-effector TCP movements. This, combined with a rigid connection between the steering column and the robot, facilitates highly accurate testing.
Solution Advantages
Real-time Precision
The Rizon 4 robot features a force-sensing accuracy of 0.03N and a response frequency of 1kHz, resulting in a communication delay of just 1ms.
Easy-to-Deploy
Automatic trajectory planning is facilitated by a single point, enabling rapid and efficient testing. The host control system can be fully customized, making the line changeover process both cost-effective and straightforward.
Safe and Reliable
Flexiv’s adaptive robots are CE and ETL certified, ensuring the safety of human-robot collaboration while enabling flexible deployment.